Find us: Building 42, Wrest Park, Silsoe, Bedford, MK45 4HP
​Call us: +44 (0) 1525 306810
​
Email us: contact@ssau.co.uk
ACHIEVING A STAR-RATING FOR DRIFT-REDUCING NOZZLES AND EQUIPMENT IN THE UK
Introduction
​
The LERAP (Local Environmental Risk Assessment for Pesticides) scheme and star-ratings for nozzles were introduced in the UK some 20 years ago. There are many nozzles that have achieved star-ratings, and also some more complicated equipment, including shielded sprayers and air-assistance. The scheme has changed significantly since then, but the underlying principles remain the same.
​
The initial scheme allowed plant protection products to be registered with a 6 m no-spray zone adjacent to a water body (products designated LERAP A and LERAP B). This no-spray zone can be reduced for LERAP B products if either lower doses, or drift reducing nozzles were used for a 12 m swath next to the no-spray zone.
The scheme has been extended twice so that larger, non-reducible no-spray zones can now be specified and, in some cases, this also requires drift reducing nozzles to be used adjacent to the no-spray zone.
​
The star-rating classification originally included 1, 2 and 3 stars, which relate to 25%, 50% and 75% drift reduction. It became clear, soon after this was introduced, that both equipment manufacturers and users were most interested in 50% and 75% levels of drift reduction, and 25%, or 1-star, was not seen as of value. Other European member states introduced higher levels of drift reduction in their schemes – 90% and 95% - and there has been pressure to follow suit. The UK has therefore now introduced a 4-star rating (90%) and the first 4-star ratings are expected to be awarded in 2019.
​
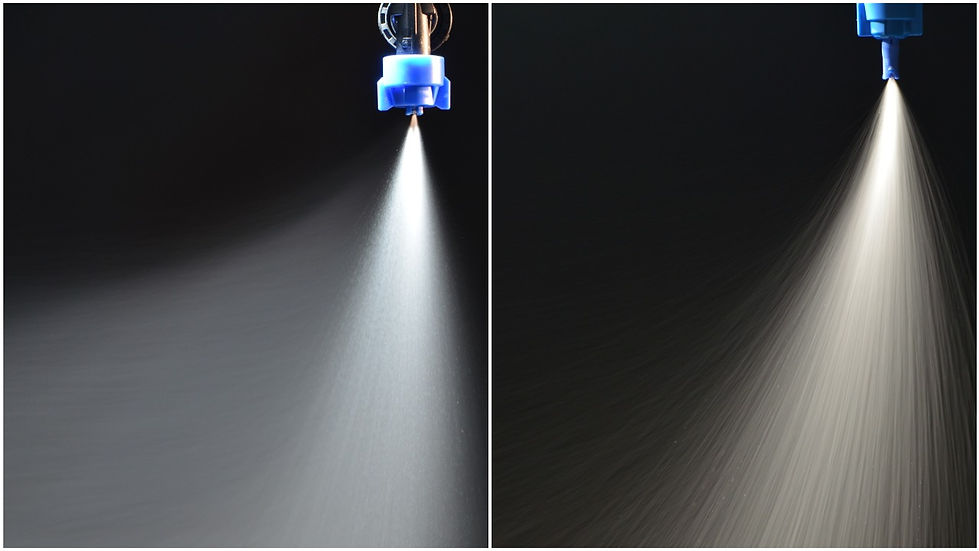
Process for achieving a star-rating
​
The UK takes a very flexible approach to this, so that any organisation can provide and supply the data on which a claim is based, or can submit a claim. Alternatively, Silsoe Spray Application Unit Ltd can provide a complete service in conducting experiments, collating and analysing the data to determine the claim that can be sought, and submitting the claim to the UK Chemicals Regulation Division (CRD).
​
Some examples of the different ways that this can be achieved are given below:
​
1. SSAU Ltd obtains data and prepares claim
​
SSAU Ltd and the customer discuss the details of the drift-reducing technology, the star-rating which the customer seeks, and the likely operating conditions where this might be achieved. This may need to be conducted under a non-disclosure agreement to protect the customer’s IP.
​
SSAU Ltd will prepare a proposal for the number of different tests that will be needed and the associated costs. This often requires several iterations to reach agreement when the proposal will be turned into a contract.
Once the contract has been agreed, the Customer will provide SSAU with the equipment and full information to allow SSAU staff to operate it correctly. For conventional hydraulic nozzles, a minimum of 20 nozzles are required of each size, from which 3 will be selected (closest to the average performance) for drift tests. For any non-standard equipment, it can be beneficial for a representative of the Customer to attend the start of the tests to check that they are happy with the way the equipment is being operated.
​
Before drift measurements are started, the equipment will be characterised. For hydraulic nozzles, this includes flow rate and droplet size across the rated pressure range.
​
The equipment will then be set up in the SSAU wind tunnel and drift measurements will be made for the agreed settings, according to an appropriate protocol. There are standard protocols available, but these might need to be modified for non-standard equipment. SSAU Ltd will be responsible for identifying the most appropriate protocol for the equipment under test. Drift measurements will also be made with the reference system, which is based on a Teejet 110 03 TP nozzle operating at 3.0 bar at 0.5 m above the drift collectors.
​
Following the measurement of drift, the data will be collated and analysed by inputting to a calculation spreadsheet which determines the drift reduction. The data and analysis are then quality checked.
The above procedures (apart from the characterisation of the equipment) are undertaken under quality standard ISO17025 for which SSAU Ltd is accredited by the United Kingdom Accreditation Service (UKAS).
​
The next step is to turn the measured drift reduction into a claim for star rating. SSAU Ltd will review the data and prepare a report to be submitted to the CRD which outlines the claim that SSAU believe can be made. This requires the Customer to provide some details of the information supplied with the equipment to the user, so that the star-rated equipment and conditions of use can be clearly identified.
​
2. The Customer or third party provides data and SSAU Ltd prepares the claim
​
If there is already good data available – either field or wind tunnel – then it may be possible to use this to create a claim. SSAU Ltd will review the data and decide whether a claim is possible, based on a number of criteria, including:
​
-
The use of an appropriate reference system;
-
Sufficient replication;
-
Adequate quality checks;
-
Measurements at a number of downwind distances;
-
Appropriate environmental conditions, including wind speed;
-
Appropriately characterised and identified equipment.
If a claim is thought to be possible, SSAU Ltd will calculate the drift reduction from the data, conduct the quality checks and prepare the report with the claim for submission to CRD.
​
3. The Customer or third party provides the data and prepares the claim
​
Under some circumstances, it might be possible for a Customer to provide a report containing the complete claim to SSAU. This will be quality checked and a short summary of the claim that SSAU believe can be recognised will be forwarded to CRD.
Whichever route is followed, if the claim is successful, CRD will then award the star rating for the equipment in a letter to the Customer and by posting the listing on the CRD website.
​
Potential costs:
Costs for the SSAU component will depend on the amount of work involved and therefore cannot be provided before initial discussions have taken place. As a very rough guide, 3 nozzle sizes tested each at three pressures might cost of the order of £10,000 for SSAU to undertake all the work outlined in (1) above. CRD currently make no charge for approving the claim.
​
How to proceed with getting a star rating for your equipment
​
In the first instance, contact Clare Butler Ellis at Silsoe Spray Applications Unit Ltd to discuss your requirements:
​
+44 (0)1525 306811
​
Updated March 2019